To enhance workplace safety in high-hazard environments, Tata Steel implemented the ‘safety eye’ system for HT line jobs and mechanical tasks to address issues such as machinery malfunctions, tool misuse, and unsafe worker behaviour. Using Internet of Things (IoT) cameras and Artificial Intelligence (AI) algorithms, the system monitors isolation of energy sources. It ensures positive isolation during job initiation and monitors the removal of isolation locks post-job. It also tracks on-job practices, detecting PPE compliance, people density, and unsafe actions like using a hammer without a finger saver or being under a hanging load.
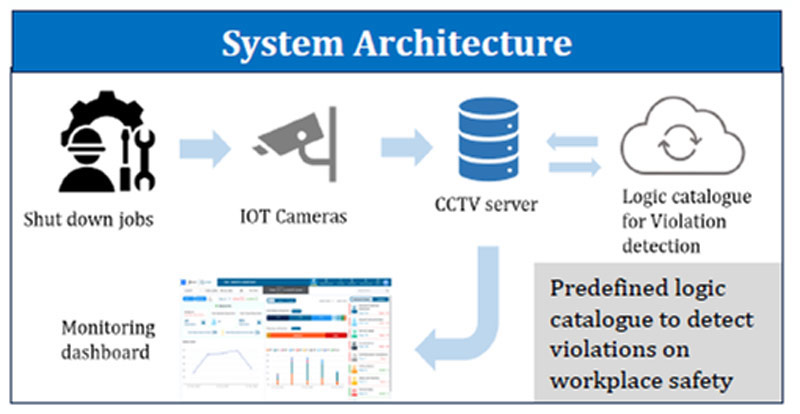
Context
One of the key aspects of workplace safety in a steel plant is isolating all energy sources before equipment maintenance. Manual interventions such as identifying, switching off, isolating, and locking/tagging energy sources can lead to errors and high severity incidents. High job volume and geographical spread on shutdown days complicate compliance monitoring for safe practices.
Benefits
Safety eye is implemented across various departments of Tata Steel Kalinganagar (TSK) and enhances safety through real-time alerts. The system was co-developed by a cross-functional team from electrical maintenance, IT, and OEM, and validated through various test cases. The team for monitoring HT jobs (IEM & safety) is trained to use the system for regular and shutdown jobs. Daily monitoring ensures immediate rectification of safety violations. In steel manufacturing, where manual energy isolation can lead to human error, safety eye`s real-time monitoring and predictive analytics help identify hazards, prevent accidents, and promote continuous improvement. Integrating the system with automation and robotics enhances safety by minimising human intervention in hazardous conditions.
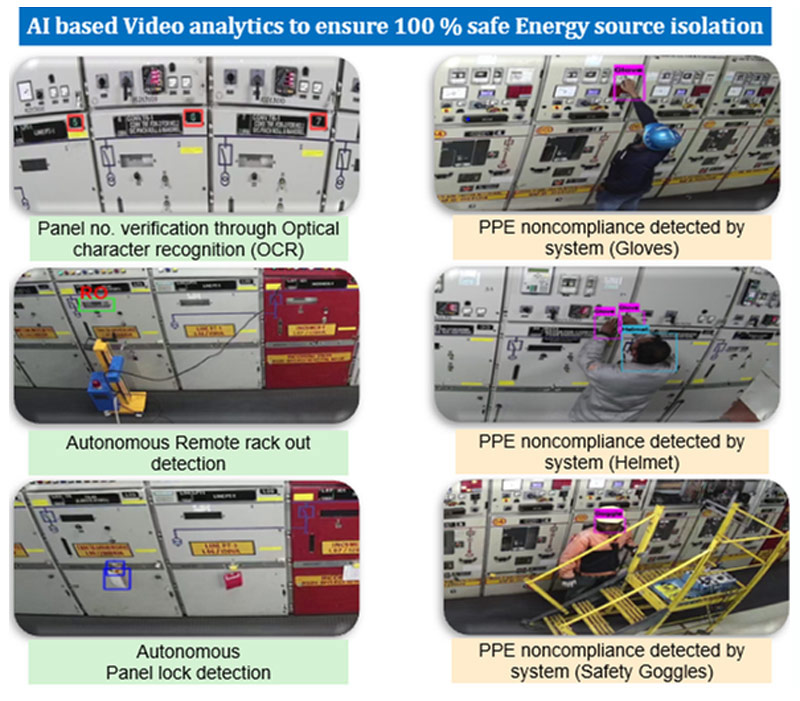