In Tata Steel’s hot strip mill, the introduction of an electromechanical rotating C-hook with 350-degree slewing and a hydraulic clamping device was implemented to address safety hazards associated with lifting defective coils. This innovative system secures coils, eliminates manual handling, and operates entirely from the crane cabin, thus enhancing safety by removing the man-machine interface and preventing potential injuries.
Context
Previously, defective coils that could not be conveyed to the storage yard were instead lifted using a mechanical C-hook, which posed significant safety risks due to human involvement. Coils were lifted without a locking mechanism, risking unwrapping, and required manual positioning. This process involved high red risk (C4, F2), highlighting the need for a safer solution. The risk is now minimised to a green level (C1, F3).
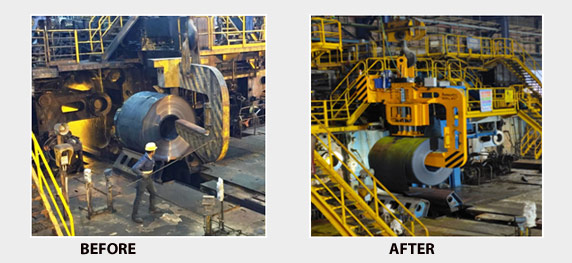
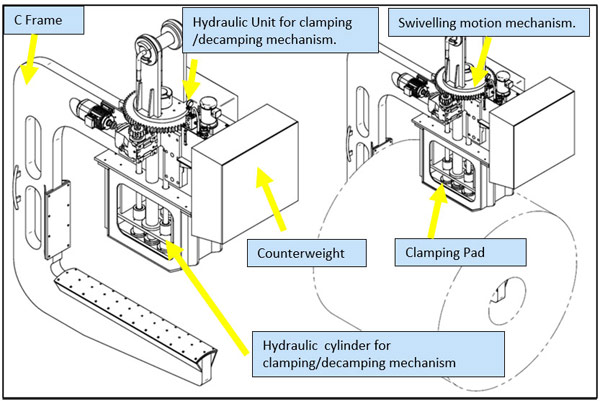
Benefits
Key features and benefits after implementation:
- Locking arrangement eliminates potential safety hazard of coil unwrapping.
- No human involvement is required during shifting and positioning of coil.
- The load arm is accurately designed for coils to be handled and rotated to the desired orientation, without human intervention.
The introduction of an electromechanical rotating C-hook has eliminated man-machine interface activities, enhancing safety in steel manufacturing. The unique design replaces traditional mechanical C-hooks, reducing risks associated with human-machine interaction and injury due to potential coil falls. Conceptualised in-house through brainstorming sessions with crane operators and supervisors, the equipment was engineered with national manufacturers.