The leadership team at Tata AutoComp Systems (TACO) has zero tolerance for safety lapses and leads from the front when it comes to the safety and health of its employees. Its key focus areas include:
- From compliance to excellence and perfection
- Focusing resources on areas where impact and risks are greatest
- Risk reviews of high-potential hazards
- Measuring, recording, reporting and analysing safety performance
The company has enhanced machine, people and plant safety across BUs by replacing the earlier practice of group safety review meetings at a centralised location with fortnightly audits or safety walks at all manufacturing locations, by rotation. The walks are conducted by a team of BU safety officers with vast cross-sector experience along with the respective BU’s leadership, maintenance and other teams. The BU safety team interacts closely with the workers and operators to understand the processes and concerns on the shopfloor, thereby assessing the progress made on the implementation of the Tata Safety & Health Management System (TSHMS).
Close interaction with the BUs has led to the inculcation of a strong spirit of ‘One TACO’, which has ensured immediate implementation of good practices while highlighting and plugging any safety pitfalls overlooked by the local team.
Purpose
To create a culture of a family-keeper by hand-holding, coaching and interacting closely with BUs. The aim is to cascade this down the organisation in order to create a self-monitoring safe environment.
Methodology
Identify – inform – initiate corrective action
- Advance charter/calendar circulated to the entire BU leadership team so that it can plan and mandatorily be available for the safety walk in the plant
- Review progress of the issues raised at previous safety walks. Highlight strengths and areas of concern that need to be addressed
- Thorough safety walk by all BU safety heads along with the respective BU head, operations and plant head, and maintenance and HR teams
- Following the plant visit, an exhaustive safety committee meeting highlights the strengths and opportunity for improvements (OFI) requiring implementation across the Group
- Circulation of MoM for corrective action within fixed timelines as per degree of criticality
Objectives
- Continuous vigilance by BU senior leadership team
- Highlight the safety pitfalls overlooked by the local team
- Improvement in challenging culture (stop it if it is unsafe)
- Improve the company’s safety culture
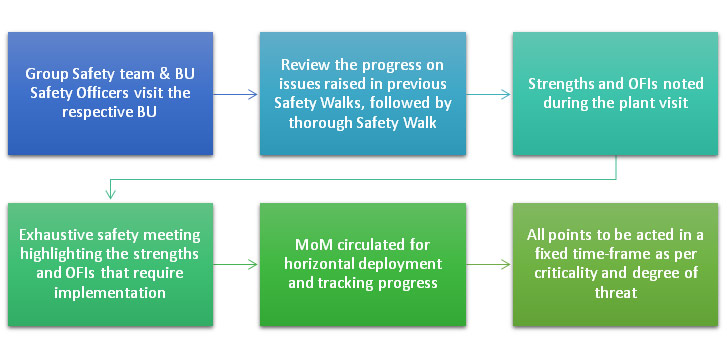
Key takeaways
- Employee participation and involvement at all levels
- Leverage expertise of safety officers in all BUs
- Frank discussions on challenges faced and immediate solutions
- Immediate lateral dissemination of best safety practices
- Improvement in behavioural-based safety of individuals
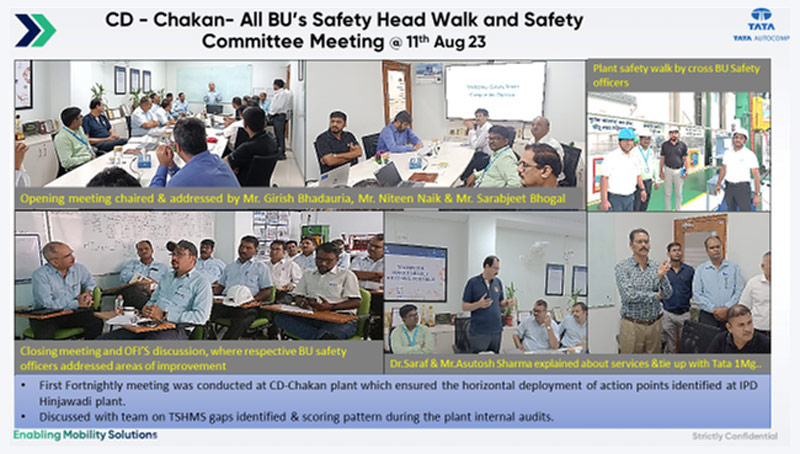
Benefits
- Enhanced all-round machine safety by providing 360-degree guarding and sensors for critical equipment
- Better safety of female employees working on machines and equipment
- Live fire drills, equipment readiness, and alertness of ERT members as well as random individuals
- Identification and mitigation of potential safety and health hazards
- Improvement in existing processes and procedures